Plasma vs. Fibre Laser – What is the Difference?
There is intense competition between plasma and laser, especially because the fibre laser has undergone further development in terms of technology and costs within just a few years. So, for the classical end user the question arises whether the fibre laser would be an alternative for their cutting jobs. Each process has its merits and technological advantages depending on the field of application.
Application
The metal-processing industry involves cutting of a wide range of different materials and sheet thicknesses. Plasma is suited for cutting metal materials, i. e. mild steel, stainless steel, aluminium, copper, brass, cast iron, foiled, or galvanised sheets and much more. In contrast to the fibre laser, plasma cutting is very flexible regarding the material quality and condition of the sheets. No special type of sheet or material pre-treatment is required, and the workpieces can be oily, greasy or rusty. The HotWire technology even allows cutting of non-conductive materials.
The possibilities of the fibre laser, however, are limited because, in part, there are high requirements on the material to be cut. There are factors that have a negative effect on the quality of the cut, i. e. rust, colour, labels, height changes, rolling defects or grooves on the surface. The upper and lower side of the material to be cut must be clean because the cut quality depends to a large degree on the sheet quality. The cutting of materials with highly reflective surfaces (aluminium, brass, copper) is also critical.
The main field of application of the laser is usually a material thickness ranging between 0.5 and 15 mm. Plasma cutting systems, in contrast, are less suited for processing thin sheets due to the powerful arc and the wider cutting kerf. They are designed for material thicknesses from 5 up to 160 mm.
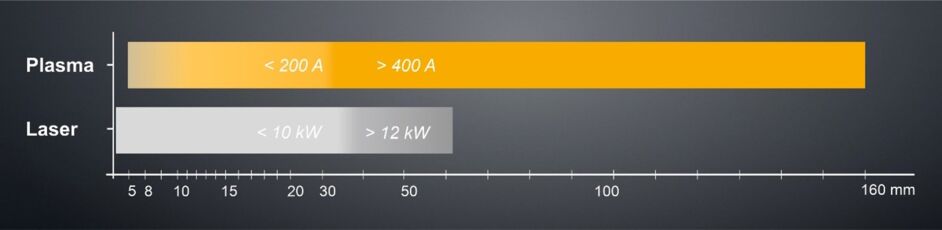
Cutting Speed
With increasing sheet thickness, the cutting speed of the laser decreases at a disproportionate rate. For material thicknesses of 10 to 15 mm and higher, the advantages of the plasma technology outweigh the laser regarding efficiency and cutting speeds.
As regards thin sheets, the fibre laser can realise a good quality at very high cutting speeds – however, very high-quality, and expensive drive and control systems are required to achieve high dynamics.

Quality
The laser is particularly suited where thin metals must be cut with highest precision and the fastest possible processing speed. Filigree contours and small geometries are among its strengths.
With plasma, a similar quality is possible; and from the medium sheet thickness range, an even better quality can be achieved, unless the parts are too fine and complex. In this case, the surface quality of a plasma cut is unmatched by the fibre laser. Plasma offers smooth and dross-free cut surfaces, high cutting speeds and cutting results with nearly no need for rework even for material thicknesses of more than 50 mm. Fine contours, narrow webs and small holes are also possible with plasma.

The surface quality of a laser cut is getting worse with increasing material thickness and surface roughness increases too. This in turn encourages the formation of a persistent oxide film on the cut surface. For subsequent processes, i. e. welding or corrosion-protection treatment (varnishing, hot-dip galvanising), rework is necessary. Due to the very small cutting kerf, there is also the risk that the kerf is filled or that the part becomes stuck or tilted.
Regarding the perpendicularity of the cut surface, the laser offers process-related advantages. However, with modern plasma cutting systems it is also possible to easily achieve angular deviations of approx. 2°; and this is perfectly acceptable for many users. Depending on the complexity and the fineness of the parts, the trailing arc may cause a slight rounding of contours during plasma cutting. Holes can be realised in good quality from a sheet thickness of 5 mm and a diameter to sheet thickness ratio of 0.75:1.
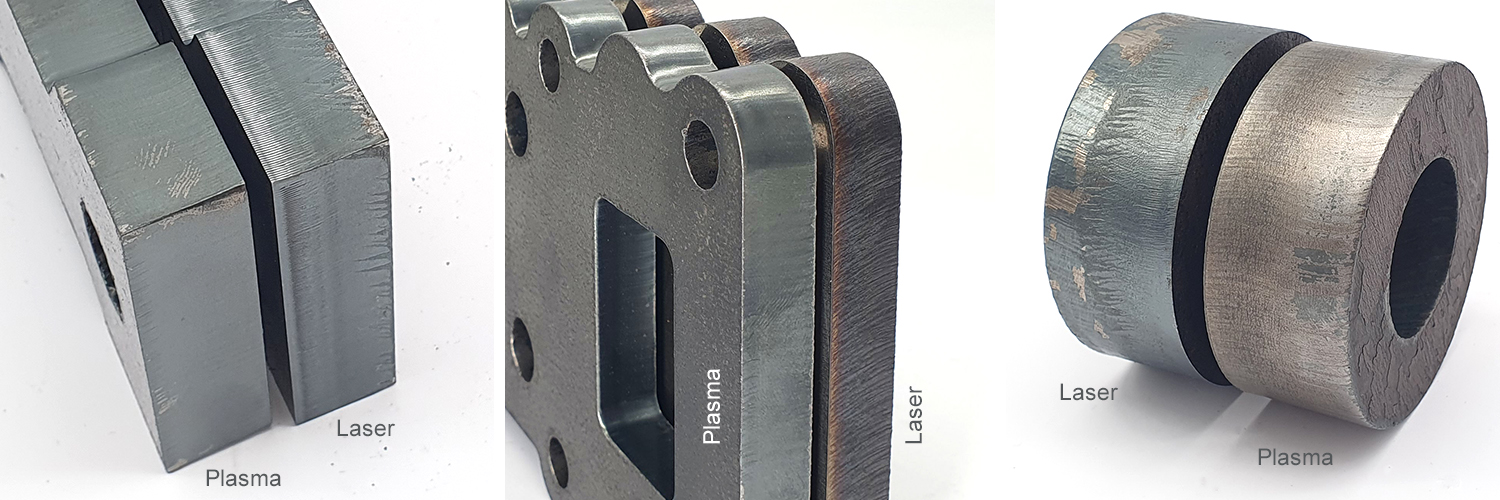
Safety & Handling
The fast and precise plasma technology has minimal safety requirements and is easy to learn and use. For the operation of a fibre laser, a high-quality safety housing is required in most parts of the world to avoid the danger from reflective laser beams. In addition, there are high safety requirements which differ from region to region, e. g. a laser safety officer. These requirements lead to comparatively high handling costs. The accessibility for loading and unloading of the cutting table as well as for maintenance is limited. In case of plasma cutting systems, flexible and simple loading and unloading is possible with forklifts, cranes, and manually, whereas laser cutting systems usually require the use of expensive and complex shuttle table systems.
With plasma cutting systems, a multi-torch operation is possible also on overlong cutting tables which could result in even higher productivity.
Angle and bevel cuts, especially multiple bevels, can still be best realised with plasma: smooth, even bevels with an angle of up to 50° with a sheet thickness ranging between 3 and 60 mm. A high-quality and reproducible production of complex multiple bevels (Y, K, X) is state of the art with modern plasma cutting systems. Due to physical reasons, however, the laser is at a disadvantage regarding bevel cutting.
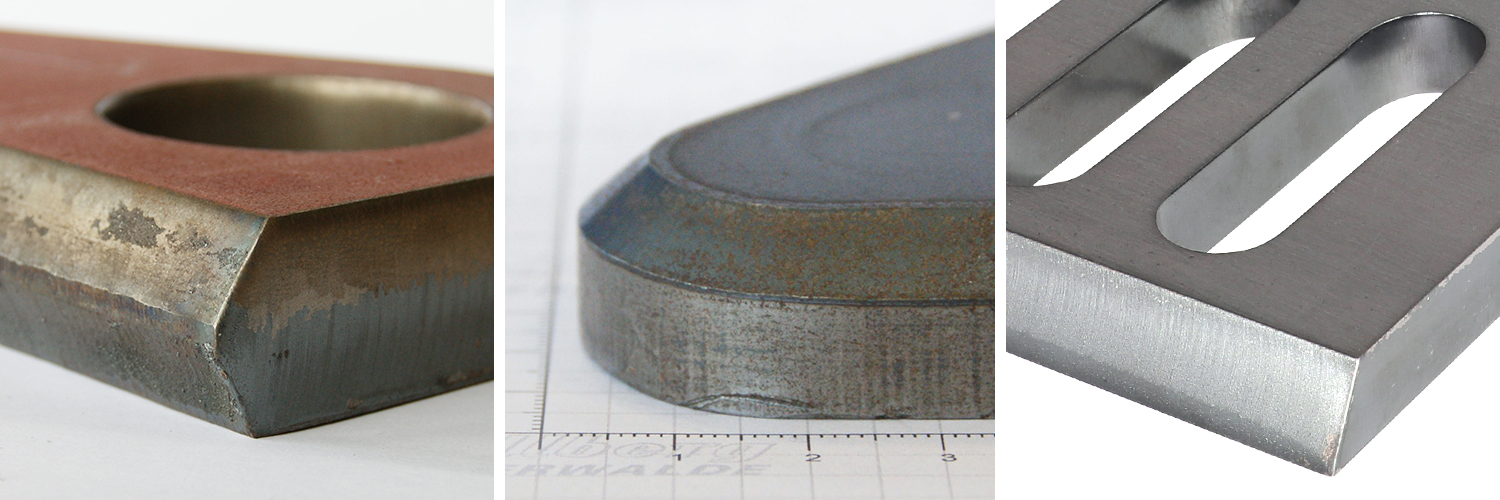
Investment & Costs
A realistic and detailed comparison of the costs of both technologies is very difficult because usually each process is used for different requirements (e. g. small contours) and operating conditions.
The cutting costs are significantly influenced by the cutting speed and the capacity utilisation which in turn depend largely on the sheet thickness. Even though the costs for consumables are lower for laser cutting systems, plasma cutting systems offer advantages regarding the gas consumption and the costs for maintenance and spare parts.
The investment costs for modern plasma cutting tables are in general significantly lower than for comparable laser cutting tables with shuttle table systems and housing.
Summary
Factor | Fibre laser | High precision plasma |
---|---|---|
Range of materials | mild steel, stainless steel, aluminium, brass, copper | |
Material requirements | high | low |
Range of material thicknesses | up to 60 mm | up to 160 mm |
Perpendicularity | ISO 1 | ISO 2 - 4 |
Parc accuracy | less than 0.05 mm | 0.2 mm - 0.5 mm |
Roughness | very high to high | low |
Minimum kerf width | 0.15 - 0.4 mm | 1 - 2.2 mm |
Cutting speed < 10 mm | faster | slower |
Cutting speed > 15 mm | slower | faster |
Investment costs | high | lower |
Operating costs | low | low |
Safety requirements | high | low |
Maintenance | moderate to high | moderate |
The team of Kjellberg Finsterwalde offers you detailed advice and will be happy to prepare a cost analysis for you.
Conclusion
Many customers use expensive laser systems although their application and requirement could be fully satisfied with plasma. Plasma cutting is a modern and future-proof technology that has become an integral part of the metalworking industry. State-of-the-art plasma systems are efficient, sustainable, powerful, and flexible.
Depending on the material type, sheet thickness, geometry, quantity, and cut quality, sometimes plasma is more efficient and sometimes laser. Before taking the final decision, it is highly recommended to thoroughly check the requirements with the help of profitability analyses.