Costs per Cutting Metre
Cutting Speed

During plasma cutting, the cutting speed has the greatest influence on the costs per cutting metre. The latest cutting technologies Contour Cut for cutting mild steel and the Ar/H2 mix technology for cutting stainless steel and aluminium on the plasma cutting systems of the HiFocus and Smart Focus series improve the cutting speeds considerably.
Example: When cutting mild steel with a material thickness of 10mm at only 90A with the systems of the HiFocus series (2,600mm/min) the speed can be nearly doubled. Applied to an 8-hour shift with 50% cutting time this means an increase of the cutting performance by 43% and a reduction of the costs per cutting metre by 31%.
Gas Consumption
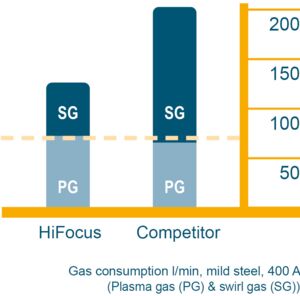
Another influencing factor on the costs per cutting metre is the gas consumption during plasma cutting. The automatic and manual gas control units made by Kjellberg Finsterwalde provide the optimum gas mixture for each cutting task. Especially in automatic gas control units the gas quantities and pressures are regulated via a database. Furthermore, the intensive liquid cooling system up to the torch tip of the PerCut torches helps achieve significant savings in the gas consumption.
Lifetime of the Consumables

Kjellberg consumables provide an excellent price-performance ratio combined with a long lifetime and, thus, have a positive influence on the costs per cutting metre and, as a result, on the operating costs. This is achieved, among other things, by the efficient liquid cooling system up to the torch tip, thus reducing the consumables consumption as well as expensive down times and thereby also the overall costs per cutting metre. HiFocus neo users can benefit from further cost advantages due to the durable and efficient copper cathodes made by Kjellberg.
Summary
The different influencing factors and their actual meaning for the costs per cutting metre:
