Principle of oxy-fuel cutting
What is oxy-fuel cutting?
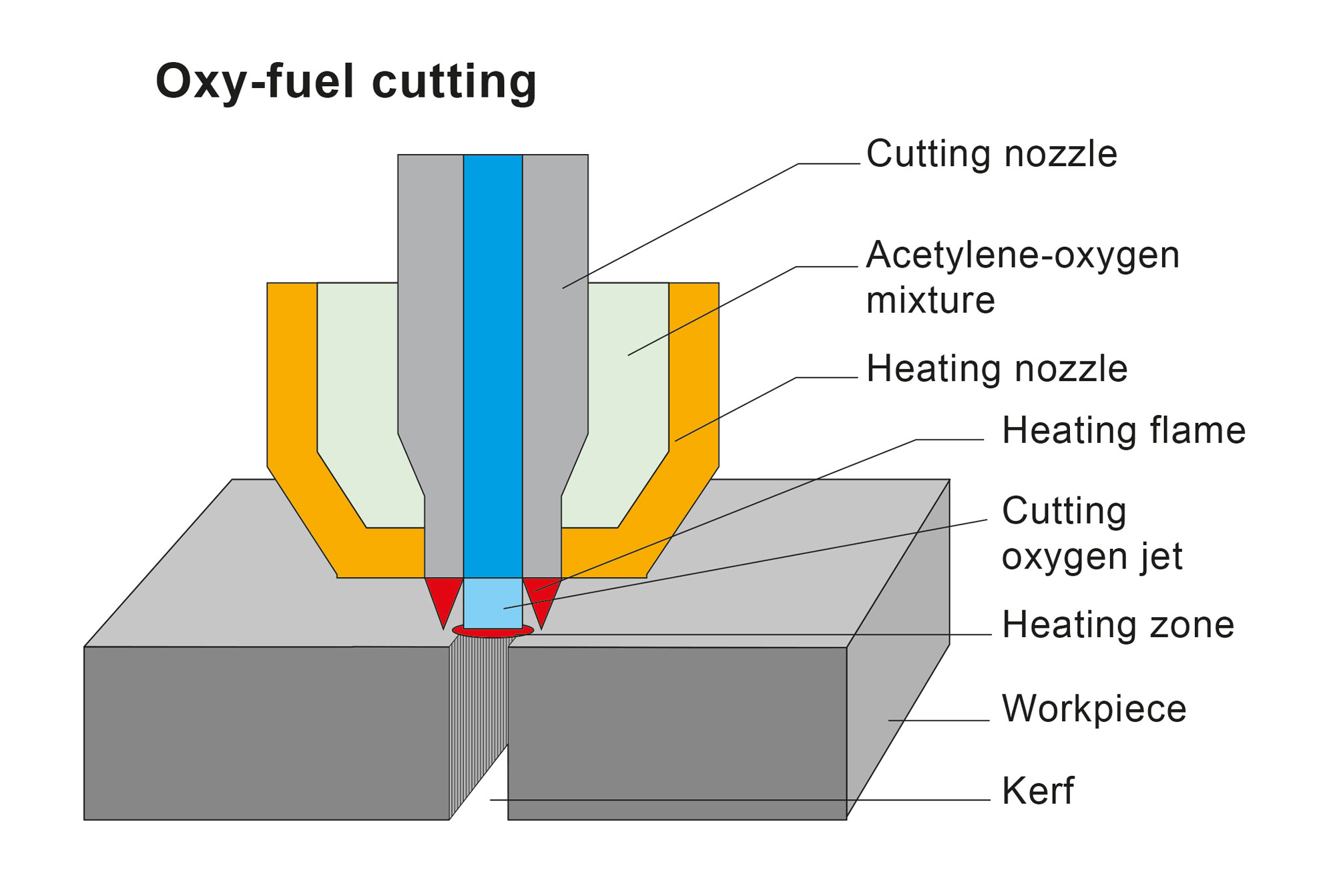
Oxy-fuel cutting is another of the thermal separation processes and is suited for unalloyed and low-alloyed steels only. An oxygen fuel gas flame heats the material to be cut to ignition temperature. The added oxygen causes the material to burn to slag, which is blown out of the kerf. The combustion reaction releases new energy which keeps the material in the kerf above ignition temperature and, thus, maintains the combustion. For the material to be suited for oxy-fuel cutting it is crucial that the ignition temperature is below its melting point and that the melting points of the oxides are below the melting point of the material so that the oxides can be blown out of the kerf in a highly fluid state.
These conditions exist particularly for unalloyed steels with very low carbon content. With increasing carbon content and increasing proportion of the alloying elements the material is less suited for oxy-fuel cutting and the cutting quality decreases. Compared to plasma and laser cutting, the process is especially suited for medium-sized and thick materials. The user benefits from low investment and consumables costs and can use several torches economically – also for bevel cutting with up to three torches on one unit. Because the heat input is high, a large heat affected zone is produced on the material. This results in material distortion, low dimensional accuracy and dross formation, which means that the cut requires reworking. Further disadvantages are the low cutting speed regarding thin and medium-sized sheets and the low piercing time.